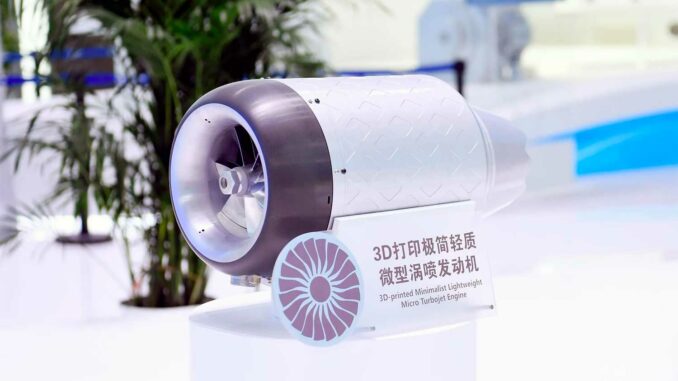
Un moteur turbojet imprimé en 3D de 160 kg de poussée a volé à 4 000 m d’altitude, validant sa stabilité pour drones et missiles légers.
La Chine a réalisé avec succès le vol d’un turboréacteur imprimé en 3D de 160 kilogrammes de poussée, conçu par AECC (Aero Engine Corporation of China). Ce moteur a atteint 4 000 mètres d’altitude lors de son essai en Mongolie intérieure. Il s’agit du premier turboréacteur chinois de cette classe à être fabriqué intégralement par conception optimisée et fabrication additive. L’objectif est double : réduire la masse, tout en maintenant des performances thermiques et mécaniques élevées. Cette avancée vise les futurs drones de reconnaissance, missiles de croisière ou plateformes autonomes de frappe légère. Le recours à l’impression 3D réduit les délais de développement, simplifie la chaîne industrielle et permet de s’affranchir de fournisseurs critiques. Ce test place la Chine au rang des rares pays capables de produire un moteur complet imprimé, testé et opérationnel.
Un vol réussi validant la fiabilité en conditions réelles
L’essai en vol du turboréacteur s’est déroulé au-dessus de la Mongolie intérieure. Le moteur a fonctionné à 4 000 mètres d’altitude, démontrant sa stabilité thermique, sa résistance structurelle, et sa capacité à supporter des variations de pression atmosphérique. Cette altitude correspond à l’environnement opérationnel typique de nombreux drones militaires de courte ou moyenne portée. La poussée de 160 kilogrammes permet d’équiper des drones tactiques ou des missiles légers, sans nécessiter d’étages de propulsion secondaires.
En comparaison, les petits moteurs turbojets utilisés sur les missiles de croisière occidentaux ou les drones MALE classiques produisent entre 150 et 300 kilogrammes de poussée pour des masses variant de 50 à 70 kilogrammes. Le moteur testé par AECC affiche donc un rapport poussée/poids compétitif, ce qui constitue un indicateur clé de performance pour les appareils embarqués.
Cette réussite marque une première en Chine : aucun autre moteur à poussée équivalente n’avait été développé en interne par fabrication additive complète, ni testé en vol. Cela permet à Pékin de renforcer sa base technologique dans les composants critiques de la motorisation aérienne légère.
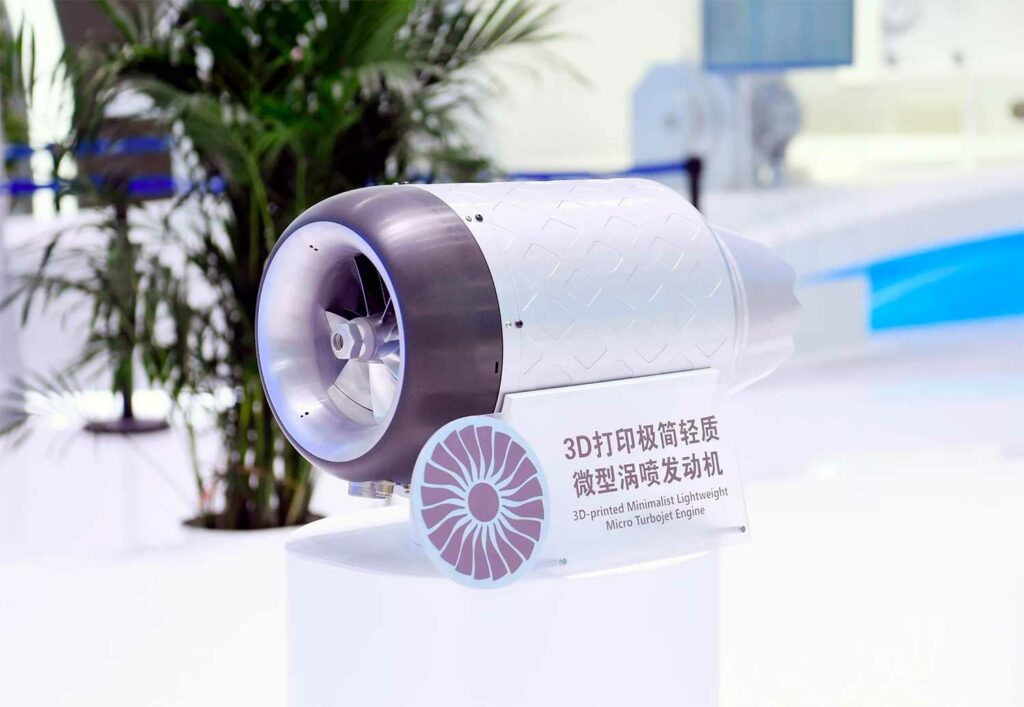
Une conception optimisée par topologie multi-disciplinaire
Le moteur a été conçu selon une méthode de topologie multi-disciplinaire, ce qui signifie que les ingénieurs ont simulé les contraintes thermiques, mécaniques et aérodynamiques avant d’imprimer chaque pièce. L’approche utilisée permet de réduire de 20 à 30 % la masse totale du moteur, tout en conservant les marges de sécurité structurelle.
Les matériaux employés, comme les alliages de titane et les superalliages à base de nickel, sont imprimés couche par couche par fusion laser, garantissant une résistance à des températures supérieures à 1 000 °C. Le procédé élimine le recours à des techniques d’assemblage traditionnelles (soudure, rivetage, brasage), ce qui limite les zones de faiblesse mécanique et réduit les délais de fabrication.
La fabrication additive intégrale permet également de réduire les délais de prototypage à quelques semaines, contre plusieurs mois en fabrication conventionnelle. Cette rapidité offre à AECC un avantage stratégique pour accélérer la mise au point de variantes ou de nouveaux modèles. D’un point de vue industriel, le moteur constitue un cas d’école : il démontre que la chaîne de production peut être simplifiée, sans compromettre les standards de fiabilité ou de performance.
Des applications immédiates pour drones tactiques et missiles
Ce type de moteur compact s’adresse à plusieurs plateformes aériennes en cours de développement en Chine. Dans le domaine des drones, il est adapté aux aéronefs de reconnaissance tactique ou aux drones d’attaque légers. Un drone de 2 tonnes équipé d’un moteur de cette classe pourrait voler à une vitesse de 600 km/h, avec une autonomie augmentée de 15 à 20 % par rapport à une motorisation conventionnelle plus lourde.
Pour les missiles, cette motorisation permettrait de concevoir des engins de 1 000 à 1 500 kilomètres de portée, volant à vitesse subsonique constante, tout en restant compacts et discrets. Le moteur pourrait également équiper des munitions rôdeuses de nouvelle génération, ou des plateformes réutilisables.
Selon les tendances du marché, les drones tactiques et les missiles intelligents représentent un segment en forte croissance : le marché global des moteurs légers pour drones est estimé à plus de 2,5 milliards d’euros d’ici 2025, avec un taux de croissance annuel proche de 12 %. En validant un moteur léger par impression 3D, la Chine se positionne pour équiper ses propres forces et proposer des solutions à l’export, notamment auprès d’alliés ou de partenaires en Asie, en Afrique ou au Moyen-Orient.
Des implications industrielles et stratégiques concrètes
Le moteur développé par AECC permet à la Chine de réduire sa dépendance technologique vis-à-vis de fournisseurs occidentaux. Jusqu’à présent, les composants critiques de propulsion pour drones ou missiles étaient souvent acquis auprès de partenaires étrangers ou copiés à partir de technologies plus anciennes. L’intégration complète d’un moteur léger en impression 3D rend possible une production locale rapide, réactive et difficile à interdire via des sanctions.
Sur le plan économique, l’impression 3D permet de réduire les coûts de production de 25 à 30 % selon les estimations disponibles, notamment en limitant les besoins en outillage, en chaînes de montage, et en logistique complexe. Cela offre une flexibilité supplémentaire pour concevoir, tester, modifier et produire des variantes adaptées à des profils de mission spécifiques.
Enfin, sur le plan stratégique, l’impression 3D de moteurs complets rend les chaînes d’approvisionnement plus résilientes. En cas de conflit ou de restriction commerciale, la fabrication additive permet de maintenir une production de guerre locale, même en environnement contraint.
Les limites technologiques et les étapes critiques restantes
Malgré ce succès en vol, plusieurs défis techniques doivent encore être surmontés avant une production industrielle à grande échelle. D’abord, la reproductibilité des pièces imprimées reste un enjeu majeur. Il est nécessaire d’intégrer des systèmes de contrôle non destructif (ultrasons, radiographie, tomographie) pour s’assurer de l’absence de défauts internes.
Ensuite, la durabilité en service devra être démontrée par des cycles d’essais en conditions extrêmes : vibrations prolongées, cycles thermiques intenses, atmosphères salines ou sablonneuses. Cela conditionne la certification pour usage militaire et, plus encore, pour un usage civil.
Enfin, l’industrie devra adapter ses normes aux spécificités de l’impression 3D. Des organismes comme la CAAC, l’EASA ou la FAA devront valider des standards pour encadrer la conception, la traçabilité et la maintenance de ce type de moteur.
La réussite du vol inaugural marque donc une avancée technique indiscutable. Mais son passage à une solution opérationnelle fiable à grande échelle dépendra de la capacité de la Chine à transformer cette démonstration en chaîne de production qualifiée, stable, et certifiée.
Avion-Chasse.fr est un site d’information indépendant.